At Productronica, November 2015, I was tasked with looking at new equipment to upgrade our existing “Direct Imaging” system at Merlin Circuit Technology Ltd and also a system for Merlin Flex Ltd; to start them on the DI journey. In the following months the leading manufacturers were invited to our facility in Deeside, North Wales, for a more detailed presentation. The benefits of some of the “LED” systems seemed obvious to us, including reduced servicing and maintenance costs combined with lower energy consumption. Of course, the primary requirements of any system would be those of positional accuracy and depth of exposure – also with many PCB designs today direct imaging of solder mask is becoming a necessity.
We already have some experience with the 4 wavelength “micromirror” (DMD) exposure heads used in the Schmoll MDI and knew they were capable of exposing standard non-DI mask whilst maintaining good sidewall profile – albeit at high energies. This along with their proven results in positional accuracy made the Schmoll MDI feature high on our list – we run 5 Schmoll drilling machines and 3 profiling/routing machines with great success.
In late 2016 the decision was made, and we took delivery of our first Schmoll MDI 4 Wave Length 2 headed machine in April 17. With good support from the MDI service centre (both onsite and online) a few weeks were spent customising the system to our requirements. Thanks to the versatility of the MDI and our CAM engineers, we were relatively quickly able to use the Schmoll for all dry film stages and some of the more challenging solder mask designs using a range of alignment targets. On completion of the initial set up and evaluation period, the MDI became a favourite with our operators – which is always a good sign! The infrared camera was a particularly useful option for reliable fiducial recognition.At the beginning of 2018 our second MDI was delivered. This time a 2 head, 2 wavelength unit. With a slightly lower cost for thephoto heads the “two wavelength” was intended for exposing dry film only. Despite the reduced number of wavelengths, after testing, good results were seen on DI solder mask as well. This MDI has now been relocated to Merlin Flex ltd, which is Merlin PCB Group’s dedicated Flex and Flex Rigid facility based in Hartlepool – where they are already seeing major benefits using DI technology.
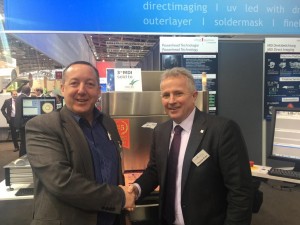
Neil Martin and Thomas Kunz the owner of Schmoll Maschinen GmbH, at Productronica Munich excepting the third MDI sold to Merlin.
Our third MDI was installed in April 2018 (2 head 4WL) and it’s clear that with each new unit,subtle improvements are being made to the operating software. We too can modify aspects of our output data in order to optimise and fully utilise the options available. Whilst the aim is to become 100% Direct Imaging there will always be the need for the occasional photo tool, be it for drill/rout check or silk screen stencil. For this reason, we have recently begun imaging contact photo tools using MDI. Already we are seeing improved image registration in comparison to our conventional laser plots, particularly in conjunction with our camera aligned contact printer. All in all, we are very happy with the MDI systems from Schmoll, which have taken us to the next level as far as bespoke imaging is concerned. It has not been without the occasional hurdle to overcome, but as expected the customer and technical support from Schmoll has been excellent.
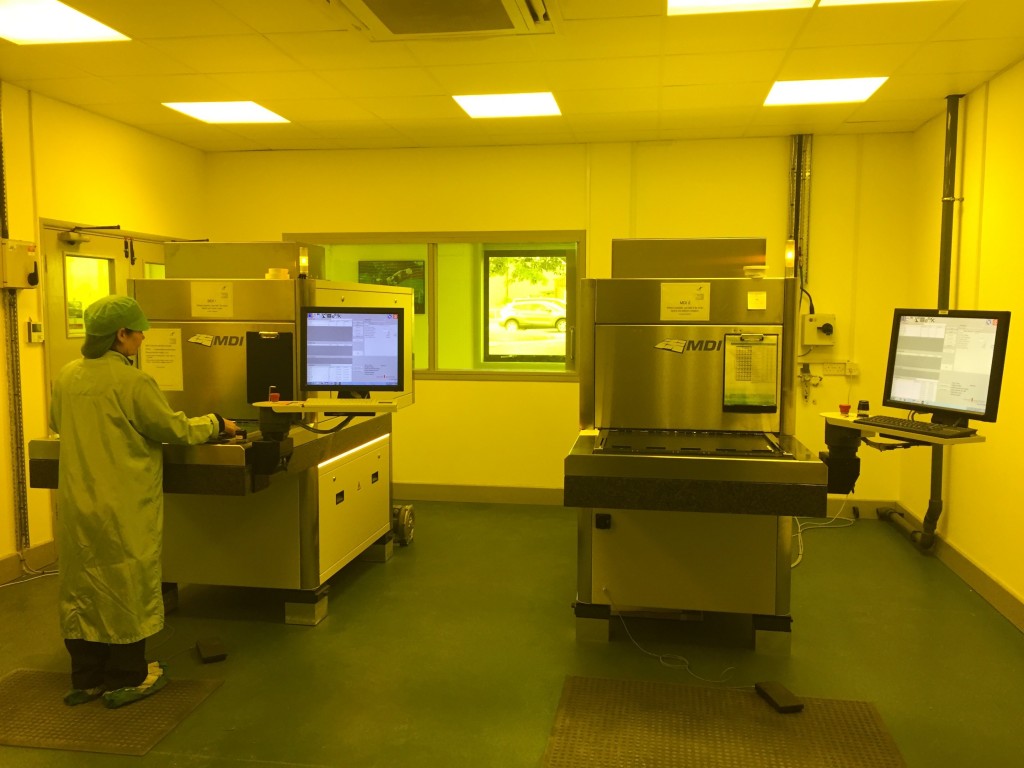
Schmoll MDI at Merlin Circuit Technology
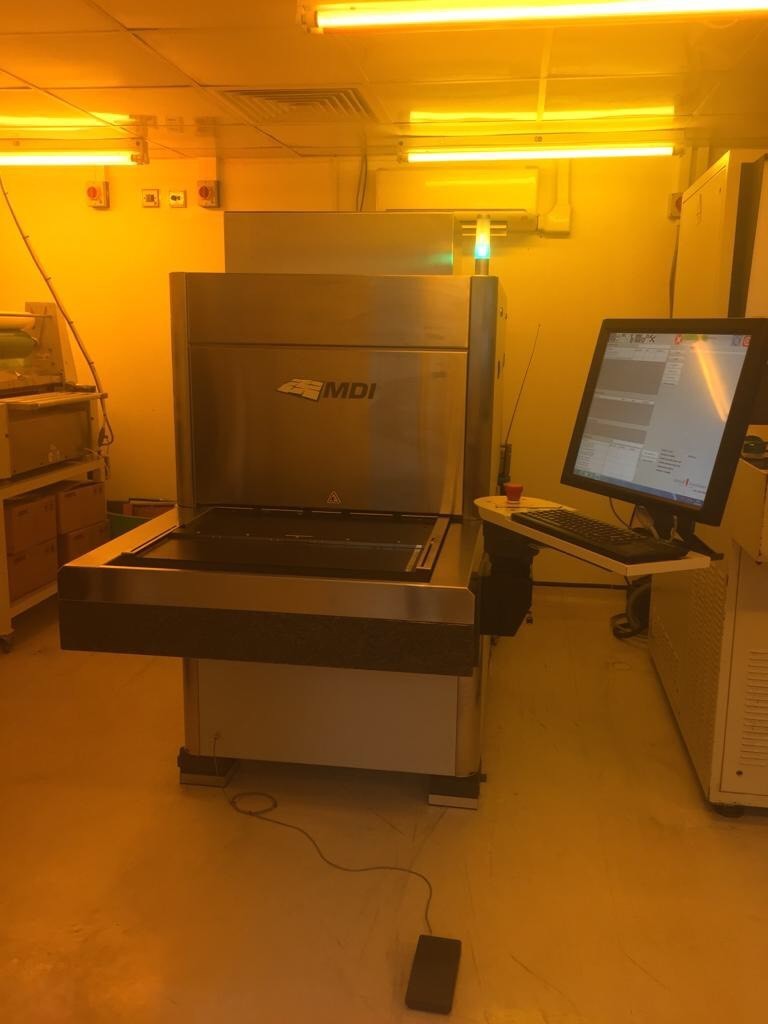
Schmoll MDI at Merlin Flex
Spencer Keene
Technical Engineer MCT